Как нам удаётся выпускать 4 завода в неделю?
Вы увидите, сколько времени и сил требуется на изготовление каждого комплекта оборудования и почему наше оборудование стоит своих денег.
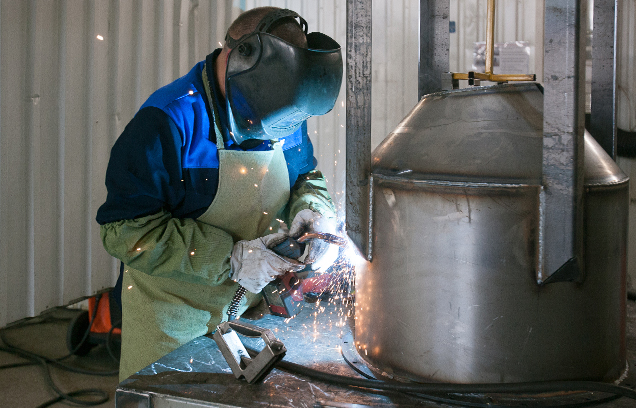
Процесс производства – от проекта до отгрузки
1. Разработка проекта
Первый проект оборудования мы разработали 14 лет назад. С тех пор было внедрено несколько десятков обновлений, появились новые виды линий и новые способы производства. Рабочим уже давно не приходится придумывать на ходу, потому что весь процесс производства до мелочей описан в конструкторской документации.

Сейчас проект для каждого вида оборудования имеет совершенный вид — этап разработки завершён ещё до поступления заказа.
Как только из отдела продаж поступает информация о продаже очередной линии, инженеры-конструкторы тут же готовят задание на производство с учётом всех пожеланий заказчика. Уже на следующий день на производстве приступают к выполнению заказа.
- ✓ Сколько времени ушло на разработку идеального проекта? 14 лет.
- ✓ Сколько нужно теперь для запуска проекта в работу? Всего 2 часа.

Каждая линия состоит из нескольких сотен больших и малых деталей. Все комплектующие должны быть готовы в нужном количестве к началу сборки линии. За эту задачу отвечает отдел снабжения. Когда поступает информация о новом заказе, отдел готовит заявку для десятков наших поставщиков. В назначенное время детали поступают на наш склад.

- ✓ Время на подготовку деталей – 2-3 часа.
В то же время инженеры готовят программы для лазерной резки металла – на изготовление нужного количества деталей.

Сейчас это чуть ли не самый приятный процесс производства – резка и гибка выполняются на немецком оборудовании фирмы Trumpf. В это оборудование мы инвестировали более 1 млн $, но это повысило качество выпускаемой продукции до высочайшего уровня. Точность обработки деталей не превышает 0,1 мм.
Лазер приносит и другие выгоды:
- работа идёт в 3-4 раза быстрее;
- исключена вероятность брака детали;
- срезы выходят идеально ровными – это упрощает сборку оборудования.
Время на лазерную обработку – 1-2 часа.
3. Сварочные и сборочные работы
В соответствии с графиком все детали попадают в сварочно-сборочный цех. Здесь с точностью ювелиров работают сварщики и слесари 5-6 разряда. Одна из главных задач – соблюдать соответствие конструкторской документации.
К слову – у сварщиков 6-й разряд считается самым высоким, и получить такой можно только после многолетнего опыта работы со сваркой газопроводов высокого давления или подводных лодок.

Ещё один секрет качественной сварки – финские сварочные аппараты Kemppi. Они обеспечивают идеально ровный и качественный сварочный шов даже в труднодоступных местах.

- ✓ В итоге – время на сварку 2-3 часа.

Как только оборудование выходит из сборочного цеха, оно попадает в покрасочную камеру. Здесь все детали обезжириваются и окрашиваются автомобильными акриловыми красками в фирменный синий цвет компании «АлтайСтройМаш».

После покраски на оборудование устанавливаются оставшиеся комплектующие (двигатель, электропроводка и прочее) и рабочие приступают к упаковке.
Даже на упаковку в нашей компании есть отдельный пакет документации, в соответствии с которым все и должно быть сделано. Это позволяет свести к минимуму вероятность повреждения при транспортировке и хранении.

- ✓ Время на покраску и упаковку – 3 часа.

На складе готовые комплекты хранятся до тех пор, пока для их отправки отдел логистики не найдет подходящий транспорт. Паузы между производством и отгрузкой не выгодны ни заводу, ни потребителю. Поэтому транспорт начинают подыскивать за 1-2 дня до поступления на склад готового комплекта оборудования.

- ✓ Время на отгрузку – 2-3 дня.
Как нам пригодился опыт Toyota?
Вернёмся к началу — что общего у нашего завода с компанией Toyota?
«АлтайСтройМаш» так же, как и компания Toyota, придерживается принципов бережливого производства на всех этапах и стремится к постоянному совершенствованию. Стремление означает действие — каждый год у нас в компании внедряется более 300 рацпредложений по улучшению продукции . Это позволяет ускорять процесс производства, снижать себестоимость продукции и улучшать качество.
Теперь вы знаете полный цикл производства – от замысла инженеров до полного воплощения в готовой продукции. Производство одной линии занимает 1-2 дня. Это время увеличивается, когда производство загружено и постоянно поступают новые заказы. С учётом этих условий линия готовится к выпуску от 3 дней до 2-3 недель.
Какие выводы можно сделать, изучив производство «АлтайСтройМаш»?
Мы рассказали вам о производстве, чтобы подтвердить 5 фактов о своей компании.
- Наивысшее качество продукции – менее 1% брака. Не даром мы даем 2 года гарантии.
- Компания выпускает профессиональное оборудование, рассчитанное на долгую бесперебойную работу – в отличие от самодельного и собранного в кустарных условиях.
- “АлтайСтройМаш” быстро производит даже крупное оборудование и без ущерба для качества.
- Бережливое производство по принципу компании Toyota. Мы научим вас вести такой же эффективный бизнес.
- Дорогие технологии могут быть полезны. Если вы хотите построить стабильный бизнес, то не стоит гнаться за дешевым оборудованием, которое подведёт в самый неподходящий момент. Убытки станут гораздо больше, чем разница в стоимости.
Именно так «АлтайСтройМаш» каждую неделю выпускает минимум по 4 крупных завода и по 20 мини-линий. Как видите, всего одно грамотное производство обеспечивает ещё более 100 крупных и 1000 мелких успешных производств за год по всему миру.
Может и вам пора заработать на производстве? Узнайте, какой вид линии стал самым востребованным и рентабельным за прошедший год.
Алексей Бурдовицын

Основатель и генеральный директор компании «АлтайСтройМаш».